Dredgers may be broadly classified into two main groups or types depending upon the method used to transport loosened material from the sea-bed to the water surface. These are :
a. Mechanical dredgers;
b. Hydraulic dredgers.
Not all dredgers fall neatly into these classifications so it is convenient to include a third, which can best be described as ‘other types’. These dredgers are usually small, sometimes unique, and normally intended for quite specific dredging or disposal situations.
A stationary dredger, moored on anchors or on spudpoles. The dredging tool is a grab normally consisting of two halfshells operated by wires or (electro)-hydraulically. The grab can be mounted on a dragline or on a hydraulic excavator of the backhoe type. Many modifications of grabs have been constructed like (top) open grab, (top) closed grabs and watertight grabs. The grab dredger is used in harbours; the dragline type also in deep water. The dredged material is loaded in barges.
Not all dredgers fall neatly into these classifications so it is convenient to include a third, which can best be described as ‘other types’. These dredgers are usually small, sometimes unique, and normally intended for quite specific dredging or disposal situations.
A stationary dredger, moored on anchors or on spudpoles. The dredging tool is a grab normally consisting of two halfshells operated by wires or (electro)-hydraulically. The grab can be mounted on a dragline or on a hydraulic excavator of the backhoe type. Many modifications of grabs have been constructed like (top) open grab, (top) closed grabs and watertight grabs. The grab dredger is used in harbours; the dragline type also in deep water. The dredged material is loaded in barges.
.
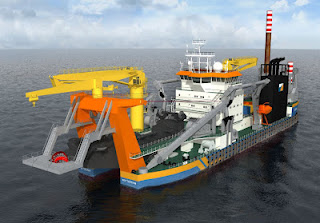
BACKHOE/DIPPER DREDGER
Backhoe and dipper dredgers again consist of a rectangular pontoon, on which is mounted the excavator unit. The excavator can be either an integral part of the dredger or a proprietary mobile type adapted for marine working. Material is excavated using a bucket of size compatible with the in-situ strength of the material being dredged. The excavated material is either loaded into barges or placed ashore. The older form of this type of dredger, the dipper or face shovel, used a wire operated integral excavator and was very heavily built to allow for dredging of hard materials such as old masonry and unblasted rock.
The wire operated excavator unit has now been largely superseded by hydraulically operated backhoe machines. These operate more efficiently than the face shovel. The size of a backhoe dredger is described by the bucket capacity, which can vary between 0.5 and 13 m3. Production is dependent upon bucket size and the hardness of the material. Breakout forces in excess of 90 t can be exerted by the larger machines, and because of the very high horizontal loads developed by the jigging action the backhoe dredger usually works on spuds. These are heavy pile-like structures which can be dropped into the sea-bed by the dredger. Two spuds are mounted at the digging end of the backhoe pontoon to provide resistance and one backhoe excavator is very efficient and has good vertical and horizontal control; carefully worked it will produce a smooth profile. Because the bucket is heavy and relatively rigid, care needs to be taken to avoid damage to such features as quay walls and canal linings.
Backhoe and dipper dredgers again consist of a rectangular pontoon, on which is mounted the excavator unit. The excavator can be either an integral part of the dredger or a proprietary mobile type adapted for marine working. Material is excavated using a bucket of size compatible with the in-situ strength of the material being dredged. The excavated material is either loaded into barges or placed ashore. The older form of this type of dredger, the dipper or face shovel, used a wire operated integral excavator and was very heavily built to allow for dredging of hard materials such as old masonry and unblasted rock.
The wire operated excavator unit has now been largely superseded by hydraulically operated backhoe machines. These operate more efficiently than the face shovel. The size of a backhoe dredger is described by the bucket capacity, which can vary between 0.5 and 13 m3. Production is dependent upon bucket size and the hardness of the material. Breakout forces in excess of 90 t can be exerted by the larger machines, and because of the very high horizontal loads developed by the jigging action the backhoe dredger usually works on spuds. These are heavy pile-like structures which can be dropped into the sea-bed by the dredger. Two spuds are mounted at the digging end of the backhoe pontoon to provide resistance and one backhoe excavator is very efficient and has good vertical and horizontal control; carefully worked it will produce a smooth profile. Because the bucket is heavy and relatively rigid, care needs to be taken to avoid damage to such features as quay walls and canal linings.
b. Hydraulic Dredger
The principal feature of all dredgers in this category is that the loosened material is raised from its in-situ state in suspension through a pipe system connected to a centrifugal pump. Various means can be employed to achieve the initial loosening of the material. If it is naturally very loose, suction alone may be sufficient, but firmer material may require mechanical loosening or the use of water jets. Hydraulic dredging is most efficient when working with fine materials, because they can easily be held in suspension. Coarser materials – and even gravel – can be worked but with a for greater demand on pump power and with greater wear on pumps and pipes.
SUCTION DREDGER
A stationary dredger used to mine for sand. The suction pipe is pushed vertically into a sand deposited. If necessary water jets help to bring the sand up. It is loaded into barges or pumped via pipeline directly to the reclamation area.
PROFILE OR PLAIN SUCTION DREDGER
In its most simple form this type consists of a pontoon able to support a pump and suction pipe and to make the connection to the discharge pipe. More sophisticated vessels have separate suction and delivery pumps, water jets at the suction inlet and articulated suction pipes. While working, a dredger may be held in position by one or more spuds or, in deeper water, by a complex system of moorings. Plain suction dredgers are mainly used to win fill material for reclamation, with the material being placed ashore through a floating pipeline. Very long distances can be pumped by the addition of booster pumps in the line. Material may alternatively be loaded directly into barges moored alongside. The normal measures of size are the diameter of the discharge pipe, which can vary between 100 and 1000 mm, or the installed horsepower.
In its most simple form this type consists of a pontoon able to support a pump and suction pipe and to make the connection to the discharge pipe. More sophisticated vessels have separate suction and delivery pumps, water jets at the suction inlet and articulated suction pipes. While working, a dredger may be held in position by one or more spuds or, in deeper water, by a complex system of moorings. Plain suction dredgers are mainly used to win fill material for reclamation, with the material being placed ashore through a floating pipeline. Very long distances can be pumped by the addition of booster pumps in the line. Material may alternatively be loaded directly into barges moored alongside. The normal measures of size are the diameter of the discharge pipe, which can vary between 100 and 1000 mm, or the installed horsepower.
Another use of plain suction dredgers – common in the USA – is to dredge from the navigation channel of a river and side cast the material to nearer the bank through a short pipeline or simply by jetting. In this role they are more commonly known as dust-pan dredgers.
Modern suction dredgers can recover material from great depths and can also extract sand from below a clay overburden. Known as a deep suction dredger, this type offers the potential to recover fill material from depths up to 100 m. Production is very dependent upon the permeability of the material dredged and is best in clean sands.
CUTTER SUCTION DREDGER
A stationary dredger which makes use of a cutter head to loosen the material to be dredged. It pumps the dredged material via a pipeline ashore or into barges. While dredging the cutter head describes arcs and is swung around the spudpole powered by winches. The cutter head can be replaced by several kinds of suction heads for special purposes, such as environmental dredging.
When the in-situ material is too compact to be removed by suction action alone, some form of mechanical loosening must be incorporated near the suction mouth. The most common method is a rotating cutter; the main feature of the cutter suction dredger. This is mounted at the lower end of the ladder used to support the cutter drive and the suction pipe. The loosened material then enters the suction mouth, passes through the suction pipe and pump (or pumps) and into the delivery line.
Cutter suction dredgers operate by swinging about a central working spud using moorings leading from the lower end of the ladder to anchors. By pulling on alternate sides the dredger clears an arc of cut, and then moves forward by pushing against the working spud using a spud carriage. A generally smooth bottom can be achieved, and modern instrumentation allows profiles and side slopes to be dredged accurately. Some of the larger cutter suction dredgers are self-propelled to allow easy movement from site to site.
The size of a cutter suction dredger is measured by the diameter of the suction pipe and by the installed machinery power. Pipe diameters are in the range 100 to 1500 mm. A modern highly automated cutter suction dredger is capable of achieving high outputs over sustained periods and production rates of around 500000 m3/week are possible under good conditions.
Cutter suction dredgers can be used to deliver through a pipe- line or to load barges. They may also be used simply as loosening devices for material to be re-handled by another type of dredger, in which mode discharge is directly over the stern to the sea. Pipeline discharge is most common but is vulnerable to waves and currents and causes an obstruction to other vessels. To avoid these problems part of the pipeline may be submerged and laid on the channel-or sea-bed.
Cutter suction dredgers are mainly used for capital dredging, especially when reclamation is associated with the dredging. Smaller vessels can be dismantled into sections and moved by road or rail for work in inland waterways, sludge lagoons, reservoirs and similar isolated areas. Large heavy-duty cutter dredgers are capable of dredging some types of rock which have not been pre-treated.
An alternative form of loosening is the use of a rotating bucket wheel at the suction mouth. Bucket wheel dredgers are most commonly used in mineral dredging operations and to date have not found general favour among the major international dredging contractors.
Cutter suction dredgers operate by swinging about a central working spud using moorings leading from the lower end of the ladder to anchors. By pulling on alternate sides the dredger clears an arc of cut, and then moves forward by pushing against the working spud using a spud carriage. A generally smooth bottom can be achieved, and modern instrumentation allows profiles and side slopes to be dredged accurately. Some of the larger cutter suction dredgers are self-propelled to allow easy movement from site to site.
The size of a cutter suction dredger is measured by the diameter of the suction pipe and by the installed machinery power. Pipe diameters are in the range 100 to 1500 mm. A modern highly automated cutter suction dredger is capable of achieving high outputs over sustained periods and production rates of around 500000 m3/week are possible under good conditions.
Cutter suction dredgers can be used to deliver through a pipe- line or to load barges. They may also be used simply as loosening devices for material to be re-handled by another type of dredger, in which mode discharge is directly over the stern to the sea. Pipeline discharge is most common but is vulnerable to waves and currents and causes an obstruction to other vessels. To avoid these problems part of the pipeline may be submerged and laid on the channel-or sea-bed.
Cutter suction dredgers are mainly used for capital dredging, especially when reclamation is associated with the dredging. Smaller vessels can be dismantled into sections and moved by road or rail for work in inland waterways, sludge lagoons, reservoirs and similar isolated areas. Large heavy-duty cutter dredgers are capable of dredging some types of rock which have not been pre-treated.
An alternative form of loosening is the use of a rotating bucket wheel at the suction mouth. Bucket wheel dredgers are most commonly used in mineral dredging operations and to date have not found general favour among the major international dredging contractors.
TRAILING SUCTION HOPPER DREDGER
A self propelled ship which fills its hold or hopper during dredging, while following a pre-set track. The hopper can be emptied by o bottom doors or valves (dumping) or by pumping its load ashore. This kind of dredger is mainly used in open water: rivers, canals, estuaries and the open sea.
Trailing suction hopper dredgers, commonly known simply as ‘hoppers’ or ‘trailers’, have a hull in the shape of a conventional ship, and are both highly seaworthy and able to operate without any form of mooring or spud. They are equipped with either single or twin (one on each side) trailing suction pipes. Material is lifted through the trailing pipes by one or more pumps and discharged into a hopper contained within the hull of the dredger. The measure of size of a hopper or trailer dredger is the hopper capacity. This may range from a few hundred cubic metres to over 20000 m’ – increasingly larger vessels have been constructed in recent years to allow economic transport of the dredged material, especially for reclamation projects.
The suction pipe terminates in a draghead, which may be of the plain type or may incorporate a water jet system, blades or teeth, or other means of dislodging compacted material. The function of the draghead is to allow the material to flow to the suction inlet as efficiently as possible.
A trailing suction hopper dredger operates very much like a floating vacuum cleaner. It sails slowly over the area to be dredged filling its hopper as it proceeds. On completion of loading the dredger sails to the disposal site where the cargo can be discharged, either by opening the doors or valves in the hopper bottom, by using the dredging pump to deliver to a shore pipeline, or directly to shore by using a special bow jet. This last technique is known as rainbowing and is commonly used for reclamation and beach nourishment.
Some trailer dredgers split over their entire length to achieve a rapid discharge of material which may be difficult to discharge through doors. Such special vessels are understandably more expensive to build than those with a rigid hull.
A self propelled dredger which brings the sediment to be excavated into suspension with waterjets. This suspension is denser than water. It will be carried away by gravity and currents. Water injection dredging is mainly used for maintenance in harbours.A self propelled dredger which brings the sediment to be excavated into suspension with waterjets. This suspension is denser than water. It will be carried away by gravity and currents. Water injection dredging is mainly used for maintenance in harbours.
Trailing suction hopper dredgers, commonly known simply as ‘hoppers’ or ‘trailers’, have a hull in the shape of a conventional ship, and are both highly seaworthy and able to operate without any form of mooring or spud. They are equipped with either single or twin (one on each side) trailing suction pipes. Material is lifted through the trailing pipes by one or more pumps and discharged into a hopper contained within the hull of the dredger. The measure of size of a hopper or trailer dredger is the hopper capacity. This may range from a few hundred cubic metres to over 20000 m’ – increasingly larger vessels have been constructed in recent years to allow economic transport of the dredged material, especially for reclamation projects.
The suction pipe terminates in a draghead, which may be of the plain type or may incorporate a water jet system, blades or teeth, or other means of dislodging compacted material. The function of the draghead is to allow the material to flow to the suction inlet as efficiently as possible.
A trailing suction hopper dredger operates very much like a floating vacuum cleaner. It sails slowly over the area to be dredged filling its hopper as it proceeds. On completion of loading the dredger sails to the disposal site where the cargo can be discharged, either by opening the doors or valves in the hopper bottom, by using the dredging pump to deliver to a shore pipeline, or directly to shore by using a special bow jet. This last technique is known as rainbowing and is commonly used for reclamation and beach nourishment.
Some trailer dredgers split over their entire length to achieve a rapid discharge of material which may be difficult to discharge through doors. Such special vessels are understandably more expensive to build than those with a rigid hull.
A self propelled dredger which brings the sediment to be excavated into suspension with waterjets. This suspension is denser than water. It will be carried away by gravity and currents. Water injection dredging is mainly used for maintenance in harbours.A self propelled dredger which brings the sediment to be excavated into suspension with waterjets. This suspension is denser than water. It will be carried away by gravity and currents. Water injection dredging is mainly used for maintenance in harbours.
A self propelled dredger which brings the sediment to be excavated into suspension with waterjets. This suspension is denser than water. It will be carried away by gravity and currents. Water injection dredging is mainly used for maintenance in harbours.
A relatively recent development in dredging equipment is the water injection dredger. This can be very effective in some material in order to fluidize it and create a turbidity current of higher density than the surrounding water. The bed material then moves in its own current. The system works best in mud and fine sand beds and has been used successfully in a number of port areas. Careful assessment must be made of the likely destination of the turbid water.
d. Auxiliaries
All modern dredgers are equipped with a range of sophisticated electronic control and data-logging systems appropriate to their type. These assist with positioning, loading and recording. VDU displays showing the position and attitude of a trailer draghead, cutter head, backhoe stick and bucket, or even a grab are set in front of the operator. Similar displays show in plan the location of the dredger and, where appropriate, its track and heading. Depth of cut, current dredged depth and slopes are also displayed on the same or separate monitors.
All these aids lead to increased efficiency of operation as they minimize overdredging. They reduce unnecessary travel or coverage (traversing an area already to profile) and improve the precision of dumping, particularly when forming the lower layers of a reclamation or where strict environmental controls exist.
e. Conclusion
Many different types of dredger exist, each with its advantages and disadvantages. The final choice of dredger for any cost and availability. Unless there are specific reasons for not using a particular type of dredger, the choice of type, size and number usually lies with the operator or contractor.
A self propelled dredger which brings the sediment to be excavated into suspension with waterjets. This suspension is denser than water. It will be carried away by gravity and currents. Water injection dredging is mainly used for maintenance in harbours.
A relatively recent development in dredging equipment is the water injection dredger. This can be very effective in some material in order to fluidize it and create a turbidity current of higher density than the surrounding water. The bed material then moves in its own current. The system works best in mud and fine sand beds and has been used successfully in a number of port areas. Careful assessment must be made of the likely destination of the turbid water.
d. Auxiliaries
All modern dredgers are equipped with a range of sophisticated electronic control and data-logging systems appropriate to their type. These assist with positioning, loading and recording. VDU displays showing the position and attitude of a trailer draghead, cutter head, backhoe stick and bucket, or even a grab are set in front of the operator. Similar displays show in plan the location of the dredger and, where appropriate, its track and heading. Depth of cut, current dredged depth and slopes are also displayed on the same or separate monitors.
All these aids lead to increased efficiency of operation as they minimize overdredging. They reduce unnecessary travel or coverage (traversing an area already to profile) and improve the precision of dumping, particularly when forming the lower layers of a reclamation or where strict environmental controls exist.
e. Conclusion
Many different types of dredger exist, each with its advantages and disadvantages. The final choice of dredger for any cost and availability. Unless there are specific reasons for not using a particular type of dredger, the choice of type, size and number usually lies with the operator or contractor.
.
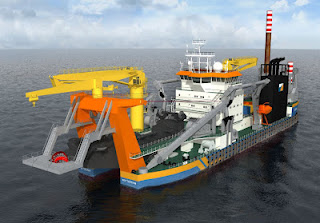
BACKHOE/DIPPER DREDGER
Backhoe and dipper dredgers again consist of a rectangular pontoon, on which is mounted the excavator unit. The excavator can be either an integral part of the dredger or a proprietary mobile type adapted for marine working. Material is excavated using a bucket of size compatible with the in-situ strength of the material being dredged. The excavated material is either loaded into barges or placed ashore. The older form of this type of dredger, the dipper or face shovel, used a wire operated integral excavator and was very heavily built to allow for dredging of hard materials such as old masonry and unblasted rock.
The wire operated excavator unit has now been largely superseded by hydraulically operated backhoe machines. These operate more efficiently than the face shovel. The size of a backhoe dredger is described by the bucket capacity, which can vary between 0.5 and 13 m3. Production is dependent upon bucket size and the hardness of the material. Breakout forces in excess of 90 t can be exerted by the larger machines, and because of the very high horizontal loads developed by the jigging action the backhoe dredger usually works on spuds. These are heavy pile-like structures which can be dropped into the sea-bed by the dredger. Two spuds are mounted at the digging end of the backhoe pontoon to provide resistance and one backhoe excavator is very efficient and has good vertical and horizontal control; carefully worked it will produce a smooth profile. Because the bucket is heavy and relatively rigid, care needs to be taken to avoid damage to such features as quay walls and canal linings.
b. Hydraulic Dredger
The principal feature of all dredgers in this category is that the loosened material is raised from its in-situ state in suspension through a pipe system connected to a centrifugal pump. Various means can be employed to achieve the initial loosening of the material. If it is naturally very loose, suction alone may be sufficient, but firmer material may require mechanical loosening or the use of water jets. Hydraulic dredging is most efficient when working with fine materials, because they can easily be held in suspension. Coarser materials – and even gravel – can be worked but with a for greater demand on pump power and with greater wear on pumps and pipes.
SUCTION DREDGER
A stationary dredger used to mine for sand. The suction pipe is pushed vertically into a sand deposited. If necessary water jets help to bring the sand up. It is loaded into barges or pumped via pipeline directly to the reclamation area.
PROFILE OR PLAIN SUCTION DREDGER
In its most simple form this type consists of a pontoon able to support a pump and suction pipe and to make the connection to the discharge pipe. More sophisticated vessels have separate suction and delivery pumps, water jets at the suction inlet and articulated suction pipes. While working, a dredger may be held in position by one or more spuds or, in deeper water, by a complex system of moorings. Plain suction dredgers are mainly used to win fill material for reclamation, with the material being placed ashore through a floating pipeline. Very long distances can be pumped by the addition of booster pumps in the line. Material may alternatively be loaded directly into barges moored alongside. The normal measures of size are the diameter of the discharge pipe, which can vary between 100 and 1000 mm, or the installed horsepower.
Another use of plain suction dredgers – common in the USA – is to dredge from the navigation channel of a river and side cast the material to nearer the bank through a short pipeline or simply by jetting. In this role they are more commonly known as dust-pan dredgers.
Modern suction dredgers can recover material from great depths and can also extract sand from below a clay overburden. Known as a deep suction dredger, this type offers the potential to recover fill material from depths up to 100 m. Production is very dependent upon the permeability of the material dredged and is best in clean sands.
CUTTER SUCTION DREDGER
A stationary dredger which makes use of a cutter head to loosen the material to be dredged. It pumps the dredged material via a pipeline ashore or into barges. While dredging the cutter head describes arcs and is swung around the spudpole powered by winches. The cutter head can be replaced by several kinds of suction heads for special purposes, such as environmental dredging.
When the in-situ material is too compact to be removed by suction action alone, some form of mechanical loosening must be incorporated near the suction mouth. The most common method is a rotating cutter; the main feature of the cutter suction dredger. This is mounted at the lower end of the ladder used to support the cutter drive and the suction pipe. The loosened material then enters the suction mouth, passes through the suction pipe and pump (or pumps) and into the delivery line.
Cutter suction dredgers operate by swinging about a central working spud using moorings leading from the lower end of the ladder to anchors. By pulling on alternate sides the dredger clears an arc of cut, and then moves forward by pushing against the working spud using a spud carriage. A generally smooth bottom can be achieved, and modern instrumentation allows profiles and side slopes to be dredged accurately. Some of the larger cutter suction dredgers are self-propelled to allow easy movement from site to site.
The size of a cutter suction dredger is measured by the diameter of the suction pipe and by the installed machinery power. Pipe diameters are in the range 100 to 1500 mm. A modern highly automated cutter suction dredger is capable of achieving high outputs over sustained periods and production rates of around 500000 m3/week are possible under good conditions.
Cutter suction dredgers can be used to deliver through a pipe- line or to load barges. They may also be used simply as loosening devices for material to be re-handled by another type of dredger, in which mode discharge is directly over the stern to the sea. Pipeline discharge is most common but is vulnerable to waves and currents and causes an obstruction to other vessels. To avoid these problems part of the pipeline may be submerged and laid on the channel-or sea-bed.
Cutter suction dredgers are mainly used for capital dredging, especially when reclamation is associated with the dredging. Smaller vessels can be dismantled into sections and moved by road or rail for work in inland waterways, sludge lagoons, reservoirs and similar isolated areas. Large heavy-duty cutter dredgers are capable of dredging some types of rock which have not been pre-treated.
An alternative form of loosening is the use of a rotating bucket wheel at the suction mouth. Bucket wheel dredgers are most commonly used in mineral dredging operations and to date have not found general favour among the major international dredging contractors.
TRAILING SUCTION HOPPER DREDGER
A self propelled ship which fills its hold or hopper during dredging, while following a pre-set track. The hopper can be emptied by o bottom doors or valves (dumping) or by pumping its load ashore. This kind of dredger is mainly used in open water: rivers, canals, estuaries and the open sea.
Trailing suction hopper dredgers, commonly known simply as ‘hoppers’ or ‘trailers’, have a hull in the shape of a conventional ship, and are both highly seaworthy and able to operate without any form of mooring or spud. They are equipped with either single or twin (one on each side) trailing suction pipes. Material is lifted through the trailing pipes by one or more pumps and discharged into a hopper contained within the hull of the dredger. The measure of size of a hopper or trailer dredger is the hopper capacity. This may range from a few hundred cubic metres to over 20000 m’ – increasingly larger vessels have been constructed in recent years to allow economic transport of the dredged material, especially for reclamation projects.
The suction pipe terminates in a draghead, which may be of the plain type or may incorporate a water jet system, blades or teeth, or other means of dislodging compacted material. The function of the draghead is to allow the material to flow to the suction inlet as efficiently as possible.
A trailing suction hopper dredger operates very much like a floating vacuum cleaner. It sails slowly over the area to be dredged filling its hopper as it proceeds. On completion of loading the dredger sails to the disposal site where the cargo can be discharged, either by opening the doors or valves in the hopper bottom, by using the dredging pump to deliver to a shore pipeline, or directly to shore by using a special bow jet. This last technique is known as rainbowing and is commonly used for reclamation and beach nourishment.
Some trailer dredgers split over their entire length to achieve a rapid discharge of material which may be difficult to discharge through doors. Such special vessels are understandably more expensive to build than those with a rigid hull.
Trailing suction hopper dredgers operate best by skimming off layers of material in long runs, such as might be found in channel dredging. They are unable to get into corners and may be difficult to manœuvre in confined spaces close to quays and jetties. They are not very effective on hard materials such as the stiffer clays, but can dredge rock which has been blasted, or loosened by a cutter dredger. These dredgers are very efficient for the materials they can handle effectively. Most harbour maintenance dredging today is carried out by trailers, and they are also employed for capital projects, pipe trenching and reclamation.
RECLAMATION DREDGER
A stationary dredger used to empty hopper barges. A suction pipe is lowered into the barge. Extra water can be added by water by water jets to facilitate the suction process. The dredged material is pumped by pipeline ashore, to a reclamation area, or to a storage depot.
BARGE UNLOADING DREDGER
Barge unloading dredgers are used to transfer material from hopper barges to shore, usually for reclamation. A barge unloader is basically a pontoon supporting a suction pump for the discharge, and a high pressure water pump used to fluidize the barge contents by jetting. The mixture is then pumped through a pipeline to the point of reclamation or disposal.
c. Other types of Dredger
Specialized types of dredger are usually of small size and output. They include simple jet-lift and air-lift, auger suction, pneumatic and amphibious dredgers.
Jet-lift dredgers use the Venturi effect of a concentrated high-speed stream of water to draw the adjacent water, together with bed material, into a delivery pipe. The jet head has no moving parts so blockage by wires and other dock debris is minimized. These dredgers are relatively small units and some can be manoeuvred on spuds alone.
Air-lift dredgers are very similar to the jet-lift dredgers but the medium for inducing water and material flow is high pressure air injected at the month of the suction pipe. As with jet-lift dredgers there are no moving parts in the flow system. Hard or other difficult to loosen materials cannot be dredged.
Augur suction dredgers operate on the same principles as a cutter suction dredger, except that the mechanical cutting tool is a rotating Archimedean screw placed at right angles to the suction pipe. The screw dislodges material, which is fed to the centrally placed suction pipe. Most units have a shroud over the cutting screw which reduces the spread of the plume of disturbed bed material which normally escapes from all dredgers. The augur suction dredger advances.into the cutting face by hauling itself along a wire deployed directly ahead. Very accurate horizontal and vertical dimensions can be achieved.
Pneumatic dredgers work on the ‘evacuator’ principle. A chamber with inlets for bed material is pumped out with the inlets closed. The inlets are then opened and water and material drawn in. The mixture is then pumped out and the cycle repeated. The unit is generally suspended from a crane on land or from a small pontoon or barge. The dredging action is intermittent and suitable only for easily flowing material.
Amphibious dredgers have the unusual feature of being able to work afloat or elevated clear of the water surface on legs. They can be equipped with grabs, buckets or a shovel installation.
All the above specialist types of dredger (and others) have been developed for specific situations and generally for small scale work such as narrow canals, industrial lagoons and reservoirs. Some types have been developed to handle contaminated sediments with minimum disturbance. They are not normally employed for large scale maintenance or capital dredging work.
A further type of dredger is the plough or bed leveller. This consists of a blade or bar which is pulled behind a suitable tug or work-boat. The method can be used for direct dredging over short distances and for levelling off the bed to the desired depth when a trailer or grab dredger is operating. It may also be used to pull material from close to quay walls and other places where a trailer cannot reach into a more accessible area. Sometimes the trailer itself operates the level1er if no tug or work-boat is available.
WATER INJECTION DREDGER
A self propelled dredger which brings the sediment to be excavated into suspension with waterjets. This suspension is denser than water. It will be carried away by gravity and currents. Water injection dredging is mainly used for maintenance in harbours.
A relatively recent development in dredging equipment is the water injection dredger. This can be very effective in some material in order to fluidize it and create a turbidity current of higher density than the surrounding water. The bed material then moves in its own current. The system works best in mud and fine sand beds and has been used successfully in a number of port areas. Careful assessment must be made of the likely destination of the turbid water.
d. Auxiliaries
All modern dredgers are equipped with a range of sophisticated electronic control and data-logging systems appropriate to their type. These assist with positioning, loading and recording. VDU displays showing the position and attitude of a trailer draghead, cutter head, backhoe stick and bucket, or even a grab are set in front of the operator. Similar displays show in plan the location of the dredger and, where appropriate, its track and heading. Depth of cut, current dredged depth and slopes are also displayed on the same or separate monitors.
All these aids lead to increased efficiency of operation as they minimize overdredging. They reduce unnecessary travel or coverage (traversing an area already to profile) and improve the precision of dumping, particularly when forming the lower layers of a reclamation or where strict environmental controls exist.
e. Conclusion
Many different types of dredger exist, each with its advantages and disadvantages. The final choice of dredger for any cost and availability. Unless there are specific reasons for not using a particular type of dredger, the choice of type, size and number usually lies with the operator or contractor.
A self propelled dredger which brings the sediment to be excavated into suspension with waterjets. This suspension is denser than water. It will be carried away by gravity and currents. Water injection dredging is mainly used for maintenance in harbours.
A relatively recent development in dredging equipment is the water injection dredger. This can be very effective in some material in order to fluidize it and create a turbidity current of higher density than the surrounding water. The bed material then moves in its own current. The system works best in mud and fine sand beds and has been used successfully in a number of port areas. Careful assessment must be made of the likely destination of the turbid water.
d. Auxiliaries
All modern dredgers are equipped with a range of sophisticated electronic control and data-logging systems appropriate to their type. These assist with positioning, loading and recording. VDU displays showing the position and attitude of a trailer draghead, cutter head, backhoe stick and bucket, or even a grab are set in front of the operator. Similar displays show in plan the location of the dredger and, where appropriate, its track and heading. Depth of cut, current dredged depth and slopes are also displayed on the same or separate monitors.
All these aids lead to increased efficiency of operation as they minimize overdredging. They reduce unnecessary travel or coverage (traversing an area already to profile) and improve the precision of dumping, particularly when forming the lower layers of a reclamation or where strict environmental controls exist.
e. Conclusion
Many different types of dredger exist, each with its advantages and disadvantages. The final choice of dredger for any cost and availability. Unless there are specific reasons for not using a particular type of dredger, the choice of type, size and number usually lies with the operator or contractor.
A self propelled dredger which brings the sediment to be excavated into suspension with waterjets. This suspension is denser than water. It will be carried away by gravity and currents. Water injection dredging is mainly used for maintenance in harbours.
A relatively recent development in dredging equipment is the water injection dredger. This can be very effective in some material in order to fluidize it and create a turbidity current of higher density than the surrounding water. The bed material then moves in its own current. The system works best in mud and fine sand beds and has been used successfully in a number of port areas. Careful assessment must be made of the likely destination of the turbid water.
d. Auxiliaries
All modern dredgers are equipped with a range of sophisticated electronic control and data-logging systems appropriate to their type. These assist with positioning, loading and recording. VDU displays showing the position and attitude of a trailer draghead, cutter head, backhoe stick and bucket, or even a grab are set in front of the operator. Similar displays show in plan the location of the dredger and, where appropriate, its track and heading. Depth of cut, current dredged depth and slopes are also displayed on the same or separate monitors.
All these aids lead to increased efficiency of operation as they minimize overdredging. They reduce unnecessary travel or coverage (traversing an area already to profile) and improve the precision of dumping, particularly when forming the lower layers of a reclamation or where strict environmental controls exist.
e. Conclusion
Many different types of dredger exist, each with its advantages and disadvantages. The final choice of dredger for any cost and availability. Unless there are specific reasons for not using a particular type of dredger, the choice of type, size and number usually lies with the operator or contractor.
A self propelled dredger which brings the sediment to be excavated into suspension with waterjets. This suspension is denser than water. It will be carried away by gravity and currents. Water injection dredging is mainly used for maintenance in harbours.
A relatively recent development in dredging equipment is the water injection dredger. This can be very effective in some material in order to fluidize it and create a turbidity current of higher density than the surrounding water. The bed material then moves in its own current. The system works best in mud and fine sand beds and has been used successfully in a number of port areas. Careful assessment must be made of the likely destination of the turbid water.
d. Auxiliaries
All modern dredgers are equipped with a range of sophisticated electronic control and data-logging systems appropriate to their type. These assist with positioning, loading and recording. VDU displays showing the position and attitude of a trailer draghead, cutter head, backhoe stick and bucket, or even a grab are set in front of the operator. Similar displays show in plan the location of the dredger and, where appropriate, its track and heading. Depth of cut, current dredged depth and slopes are also displayed on the same or separate monitors.
All these aids lead to increased efficiency of operation as they minimize overdredging. They reduce unnecessary travel or coverage (traversing an area already to profile) and improve the precision of dumping, particularly when forming the lower layers of a reclamation or where strict environmental controls exist.
e. Conclusion
Many different types of dredger exist, each with its advantages and disadvantages. The final choice of dredger for any cost and availability. Unless there are specific reasons for not using a particular type of dredger, the choice of type, size and number usually lies with the operator or contractor.
A self propelled dredger which brings the sediment to be excavated into suspension with waterjets. This suspension is denser than water. It will be carried away by gravity and currents. Water injection dredging is mainly used for maintenance in harbours.
A relatively recent development in dredging equipment is the water injection dredger. This can be very effective in some material in order to fluidize it and create a turbidity current of higher density than the surrounding water. The bed material then moves in its own current. The system works best in mud and fine sand beds and has been used successfully in a number of port areas. Careful assessment must be made of the likely destination of the turbid water.
d. Auxiliaries
All modern dredgers are equipped with a range of sophisticated electronic control and data-logging systems appropriate to their type. These assist with positioning, loading and recording. VDU displays showing the position and attitude of a trailer draghead, cutter head, backhoe stick and bucket, or even a grab are set in front of the operator. Similar displays show in plan the location of the dredger and, where appropriate, its track and heading. Depth of cut, current dredged depth and slopes are also displayed on the same or separate monitors.
All these aids lead to increased efficiency of operation as they minimize over dredging. They reduce unnecessary travel or coverage (traversing an area already to profile) and improve the precision of dumping, particularly when forming the lower layers of a reclamation or where strict environmental controls exist.
e. Conclusion
Many different types of dredger exist, each with its advantages and disadvantages. The final choice of dredger for any cost and availability. Unless there are specific reasons for not using a particular type of dredger, the choice of type, size and number usually lies with the operator or contractor.
A self propelled dredger which brings the sediment to be excavated into suspension with waterjets. This suspension is denser than water. It will be carried away by gravity and currents. Water injection dredging is mainly used for maintenance in harbours.
A relatively recent development in dredging equipment is the water injection dredger. This can be very effective in some material in order to fluidize it and create a turbidity current of higher density than the surrounding water. The bed material then moves in its own current. The system works best in mud and fine sand beds and has been used successfully in a number of port areas. Careful assessment must be made of the likely destination of the turbid water.
d. Auxiliaries
All modern dredgers are equipped with a range of sophisticated electronic control and data-logging systems appropriate to their type. These assist with positioning, loading and recording. VDU displays showing the position and attitude of a trailer draghead, cutter head, backhoe stick and bucket, or even a grab are set in front of the operator. Similar displays show in plan the location of the dredger and, where appropriate, its track and heading. Depth of cut, current dredged depth and slopes are also displayed on the same or separate monitors.
All these aids lead to increased efficiency of operation as they minimize overdredging. They reduce unnecessary travel or coverage (traversing an area already to profile) and improve the precision of dumping, particularly when forming the lower layers of a reclamation or where strict environmental controls exist.
e. Conclusion
Many different types of dredger exist, each with its advantages and disadvantages. The final choice of dredger for any cost and availability. Unless there are specific reasons for not using a particular type of dredger, the choice of type, size and number usually lies with the operator or contractor.
.
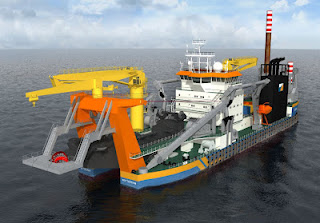
BACKHOE/DIPPER DREDGER
Backhoe and dipper dredgers again consist of a rectangular pontoon, on which is mounted the excavator unit. The excavator can be either an integral part of the dredger or a proprietary mobile type adapted for marine working. Material is excavated using a bucket of size compatible with the in-situ strength of the material being dredged. The excavated material is either loaded into barges or placed ashore. The older form of this type of dredger, the dipper or face shovel, used a wire operated integral excavator and was very heavily built to allow for dredging of hard materials such as old masonry and unblasted rock.
The wire operated excavator unit has now been largely superseded by hydraulically operated backhoe machines. These operate more efficiently than the face shovel. The size of a backhoe dredger is described by the bucket capacity, which can vary between 0.5 and 13 m3. Production is dependent upon bucket size and the hardness of the material. Breakout forces in excess of 90 t can be exerted by the larger machines, and because of the very high horizontal loads developed by the jigging action the backhoe dredger usually works on spuds. These are heavy pile-like structures which can be dropped into the sea-bed by the dredger. Two spuds are mounted at the digging end of the backhoe pontoon to provide resistance and one backhoe excavator is very efficient and has good vertical and horizontal control; carefully worked it will produce a smooth profile. Because the bucket is heavy and relatively rigid, care needs to be taken to avoid damage to such features as quay walls and canal linings.
b. Hydraulic Dredger
The principal feature of all dredgers in this category is that the loosened material is raised from its in-situ state in suspension through a pipe system connected to a centrifugal pump. Various means can be employed to achieve the initial loosening of the material. If it is naturally very loose, suction alone may be sufficient, but firmer material may require mechanical loosening or the use of water jets. Hydraulic dredging is most efficient when working with fine materials, because they can easily be held in suspension. Coarser materials – and even gravel – can be worked but with a for greater demand on pump power and with greater wear on pumps and pipes.
SUCTION DREDGER
A stationary dredger used to mine for sand. The suction pipe is pushed vertically into a sand deposited. If necessary water jets help to bring the sand up. It is loaded into barges or pumped via pipeline directly to the reclamation area.
PROFILE OR PLAIN SUCTION DREDGER
In its most simple form this type consists of a pontoon able to support a pump and suction pipe and to make the connection to the discharge pipe. More sophisticated vessels have separate suction and delivery pumps, water jets at the suction inlet and articulated suction pipes. While working, a dredger may be held in position by one or more spuds or, in deeper water, by a complex system of moorings. Plain suction dredgers are mainly used to win fill material for reclamation, with the material being placed ashore through a floating pipeline. Very long distances can be pumped by the addition of booster pumps in the line. Material may alternatively be loaded directly into barges moored alongside. The normal measures of size are the diameter of the discharge pipe, which can vary between 100 and 1000 mm, or the installed horsepower.
Another use of plain suction dredgers – common in the USA – is to dredge from the navigation channel of a river and side cast the material to nearer the bank through a short pipeline or simply by jetting. In this role they are more commonly known as dust-pan dredgers.
Modern suction dredgers can recover material from great depths and can also extract sand from below a clay overburden. Known as a deep suction dredger, this type offers the potential to recover fill material from depths up to 100 m. Production is very dependent upon the permeability of the material dredged and is best in clean sands.
CUTTER SUCTION DREDGER
A stationary dredger which makes use of a cutter head to loosen the material to be dredged. It pumps the dredged material via a pipeline ashore or into barges. While dredging the cutter head describes arcs and is swung around the spudpole powered by winches. The cutter head can be replaced by several kinds of suction heads for special purposes, such as environmental dredging.
When the in-situ material is too compact to be removed by suction action alone, some form of mechanical loosening must be incorporated near the suction mouth. The most common method is a rotating cutter; the main feature of the cutter suction dredger. This is mounted at the lower end of the ladder used to support the cutter drive and the suction pipe. The loosened material then enters the suction mouth, passes through the suction pipe and pump (or pumps) and into the delivery line.
Cutter suction dredgers operate by swinging about a central working spud using moorings leading from the lower end of the ladder to anchors. By pulling on alternate sides the dredger clears an arc of cut, and then moves forward by pushing against the working spud using a spud carriage. A generally smooth bottom can be achieved, and modern instrumentation allows profiles and side slopes to be dredged accurately. Some of the larger cutter suction dredgers are self-propelled to allow easy movement from site to site.
The size of a cutter suction dredger is measured by the diameter of the suction pipe and by the installed machinery power. Pipe diameters are in the range 100 to 1500 mm. A modern highly automated cutter suction dredger is capable of achieving high outputs over sustained periods and production rates of around 500000 m3/week are possible under good conditions.
Cutter suction dredgers can be used to deliver through a pipe- line or to load barges. They may also be used simply as loosening devices for material to be re-handled by another type of dredger, in which mode discharge is directly over the stern to the sea. Pipeline discharge is most common but is vulnerable to waves and currents and causes an obstruction to other vessels. To avoid these problems part of the pipeline may be submerged and laid on the channel-or sea-bed.
Cutter suction dredgers are mainly used for capital dredging, especially when reclamation is associated with the dredging. Smaller vessels can be dismantled into sections and moved by road or rail for work in inland waterways, sludge lagoons, reservoirs and similar isolated areas. Large heavy-duty cutter dredgers are capable of dredging some types of rock which have not been pre-treated.
An alternative form of loosening is the use of a rotating bucket wheel at the suction mouth. Bucket wheel dredgers are most commonly used in mineral dredging operations and to date have not found general favour among the major international dredging contractors.
TRAILING SUCTION HOPPER DREDGER
A self propelled ship which fills its hold or hopper during dredging, while following a pre-set track. The hopper can be emptied by o bottom doors or valves (dumping) or by pumping its load ashore. This kind of dredger is mainly used in open water: rivers, canals, estuaries and the open sea.
Trailing suction hopper dredgers, commonly known simply as ‘hoppers’ or ‘trailers’, have a hull in the shape of a conventional ship, and are both highly seaworthy and able to operate without any form of mooring or spud. They are equipped with either single or twin (one on each side) trailing suction pipes. Material is lifted through the trailing pipes by one or more pumps and discharged into a hopper contained within the hull of the dredger. The measure of size of a hopper or trailer dredger is the hopper capacity. This may range from a few hundred cubic metres to over 20000 m’ – increasingly larger vessels have been constructed in recent years to allow economic transport of the dredged material, especially for reclamation projects.
The suction pipe terminates in a draghead, which may be of the plain type or may incorporate a water jet system, blades or teeth, or other means of dislodging compacted material. The function of the draghead is to allow the material to flow to the suction inlet as efficiently as possible.
A trailing suction hopper dredger operates very much like a floating vacuum cleaner. It sails slowly over the area to be dredged filling its hopper as it proceeds. On completion of loading the dredger sails to the disposal site where the cargo can be discharged, either by opening the doors or valves in the hopper bottom, by using the dredging pump to deliver to a shore pipeline, or directly to shore by using a special bow jet. This last technique is known as rainbowing and is commonly used for reclamation and beach nourishment.
Some trailer dredgers split over their entire length to achieve a rapid discharge of material which may be difficult to discharge through doors. Such special vessels are understandably more expensive to build than those with a rigid hull.
Trailing suction hopper dredgers operate best by skimming off layers of material in long runs, such as might be found in channel dredging. They are unable to get into corners and may be difficult to manœuvre in confined spaces close to quays and jetties. They are not very effective on hard materials such as the stiffer clays, but can dredge rock which has been blasted, or loosened by a cutter dredger. These dredgers are very efficient for the materials they can handle effectively. Most harbour maintenance dredging today is carried out by trailers, and they are also employed for capital projects, pipe trenching and reclamation.
RECLAMATION DREDGER
A stationary dredger used to empty hopper barges. A suction pipe is lowered into the barge. Extra water can be added by water by water jets to facilitate the suction process. The dredged material is pumped by pipeline ashore, to a reclamation area, or to a storage depot.
BARGE UNLOADING DREDGER
Barge unloading dredgers are used to transfer material from hopper barges to shore, usually for reclamation. A barge unloader is basically a pontoon supporting a suction pump for the discharge, and a high pressure water pump used to fluidize the barge contents by jetting. The mixture is then pumped through a pipeline to the point of reclamation or disposal.
c. Other types of Dredger
Specialized types of dredger are usually of small size and output. They include simple jet-lift and air-lift, auger suction, pneumatic and amphibious dredgers.
Jet-lift dredgers use the Venturi effect of a concentrated high-speed stream of water to draw the adjacent water, together with bed material, into a delivery pipe. The jet head has no moving parts so blockage by wires and other dock debris is minimized. These dredgers are relatively small units and some can be manoeuvred on spuds alone.
Air-lift dredgers are very similar to the jet-lift dredgers but the medium for inducing water and material flow is high pressure air injected at the month of the suction pipe. As with jet-lift dredgers there are no moving parts in the flow system. Hard or other difficult to loosen materials cannot be dredged.
Augur suction dredgers operate on the same principles as a cutter suction dredger, except that the mechanical cutting tool is a rotating Archimedean screw placed at right angles to the suction pipe. The screw dislodges material, which is fed to the centrally placed suction pipe. Most units have a shroud over the cutting screw which reduces the spread of the plume of disturbed bed material which normally escapes from all dredgers. The augur suction dredger advances.into the cutting face by hauling itself along a wire deployed directly ahead. Very accurate horizontal and vertical dimensions can be achieved.
Pneumatic dredgers work on the ‘evacuator’ principle. A chamber with inlets for bed material is pumped out with the inlets closed. The inlets are then opened and water and material drawn in. The mixture is then pumped out and the cycle repeated. The unit is generally suspended from a crane on land or from a small pontoon or barge. The dredging action is intermittent and suitable only for easily flowing material.
Amphibious dredgers have the unusual feature of being able to work afloat or elevated clear of the water surface on legs. They can be equipped with grabs, buckets or a shovel installation.
All the above specialist types of dredger (and others) have been developed for specific situations and generally for small scale work such as narrow canals, industrial lagoons and reservoirs. Some types have been developed to handle contaminated sediments with minimum disturbance. They are not normally employed for large scale maintenance or capital dredging work.
A further type of dredger is the plough or bed leveller. This consists of a blade or bar which is pulled behind a suitable tug or work-boat. The method can be used for direct dredging over short distances and for levelling off the bed to the desired depth when a trailer or grab dredger is operating. It may also be used to pull material from close to quay walls and other places where a trailer cannot reach into a more accessible area. Sometimes the trailer itself operates the level1er if no tug or work-boat is available.
WATER INJECTION DREDGER
A self propelled dredger which brings the sediment to be excavated into suspension with waterjets. This suspension is denser than water. It will be carried away by gravity and currents. Water injection dredging is mainly used for maintenance in harbours.
A relatively recent development in dredging equipment is the water injection dredger. This can be very effective in some material in order to fluidize it and create a turbidity current of higher density than the surrounding water. The bed material then moves in its own current. The system works best in mud and fine sand beds and has been used successfully in a number of port areas. Careful assessment must be made of the likely destination of the turbid water.
d. Auxiliaries
All modern dredgers are equipped with a range of sophisticated electronic control and data-logging systems appropriate to their type. These assist with positioning, loading and recording. VDU displays showing the position and attitude of a trailer draghead, cutter head, backhoe stick and bucket, or even a grab are set in front of the operator. Similar displays show in plan the location of the dredger and, where appropriate, its track and heading. Depth of cut, current dredged depth and slopes are also displayed on the same or separate monitors.
All these aids lead to increased efficiency of operation as they minimize overdredging. They reduce unnecessary travel or coverage (traversing an area already to profile) and improve the precision of dumping, particularly when forming the lower layers of a reclamation or where strict environmental controls exist.
e. Conclusion
Many different types of dredger exist, each with its advantages and disadvantages. The final choice of dredger for any cost and availability. Unless there are specific reasons for not using a particular type of dredger, the choice of type, size and number usually lies with the operator or contractor.
A self propelled dredger which brings the sediment to be excavated into suspension with waterjets. This suspension is denser than water. It will be carried away by gravity and currents. Water injection dredging is mainly used for maintenance in harbours.
A relatively recent development in dredging equipment is the water injection dredger. This can be very effective in some material in order to fluidize it and create a turbidity current of higher density than the surrounding water. The bed material then moves in its own current. The system works best in mud and fine sand beds and has been used successfully in a number of port areas. Careful assessment must be made of the likely destination of the turbid water.
d. Auxiliaries
All modern dredgers are equipped with a range of sophisticated electronic control and data-logging systems appropriate to their type. These assist with positioning, loading and recording. VDU displays showing the position and attitude of a trailer draghead, cutter head, backhoe stick and bucket, or even a grab are set in front of the operator. Similar displays show in plan the location of the dredger and, where appropriate, its track and heading. Depth of cut, current dredged depth and slopes are also displayed on the same or separate monitors.
All these aids lead to increased efficiency of operation as they minimize overdredging. They reduce unnecessary travel or coverage (traversing an area already to profile) and improve the precision of dumping, particularly when forming the lower layers of a reclamation or where strict environmental controls exist.
e. Conclusion
Many different types of dredger exist, each with its advantages and disadvantages. The final choice of dredger for any cost and availability. Unless there are specific reasons for not using a particular type of dredger, the choice of type, size and number usually lies with the operator or contractor.
Trailing suction hopper dredgers operate best by skimming off layers of material in long runs, such as might be found in channel dredging. They are unable to get into corners and may be difficult to manœuvre in confined spaces close to quays and jetties. They are not very effective on hard materials such as the stiffer clays, but can dredge rock which has been blasted, or loosened by a cutter dredger. These dredgers are very efficient for the materials they can handle effectively. Most harbour maintenance dredging today is carried out by trailers, and they are also employed for capital projects, pipe trenching and reclamation.
RECLAMATION DREDGER
A stationary dredger used to empty hopper barges. A suction pipe is lowered into the barge. Extra water can be added by water by water jets to facilitate the suction process. The dredged material is pumped by pipeline ashore, to a reclamation area, or to a storage depot.
A stationary dredger used to empty hopper barges. A suction pipe is lowered into the barge. Extra water can be added by water by water jets to facilitate the suction process. The dredged material is pumped by pipeline ashore, to a reclamation area, or to a storage depot.
BARGE UNLOADING DREDGER
Barge unloading dredgers are used to transfer material from hopper barges to shore, usually for reclamation. A barge unloader is basically a pontoon supporting a suction pump for the discharge, and a high pressure water pump used to fluidize the barge contents by jetting. The mixture is then pumped through a pipeline to the point of reclamation or disposal.
Barge unloading dredgers are used to transfer material from hopper barges to shore, usually for reclamation. A barge unloader is basically a pontoon supporting a suction pump for the discharge, and a high pressure water pump used to fluidize the barge contents by jetting. The mixture is then pumped through a pipeline to the point of reclamation or disposal.
c. Other types of Dredger
Specialized types of dredger are usually of small size and output. They include simple jet-lift and air-lift, auger suction, pneumatic and amphibious dredgers.
Jet-lift dredgers use the Venturi effect of a concentrated high-speed stream of water to draw the adjacent water, together with bed material, into a delivery pipe. The jet head has no moving parts so blockage by wires and other dock debris is minimized. These dredgers are relatively small units and some can be manoeuvred on spuds alone.
Air-lift dredgers are very similar to the jet-lift dredgers but the medium for inducing water and material flow is high pressure air injected at the month of the suction pipe. As with jet-lift dredgers there are no moving parts in the flow system. Hard or other difficult to loosen materials cannot be dredged.
Augur suction dredgers operate on the same principles as a cutter suction dredger, except that the mechanical cutting tool is a rotating Archimedean screw placed at right angles to the suction pipe. The screw dislodges material, which is fed to the centrally placed suction pipe. Most units have a shroud over the cutting screw which reduces the spread of the plume of disturbed bed material which normally escapes from all dredgers. The augur suction dredger advances.into the cutting face by hauling itself along a wire deployed directly ahead. Very accurate horizontal and vertical dimensions can be achieved.
Pneumatic dredgers work on the ‘evacuator’ principle. A chamber with inlets for bed material is pumped out with the inlets closed. The inlets are then opened and water and material drawn in. The mixture is then pumped out and the cycle repeated. The unit is generally suspended from a crane on land or from a small pontoon or barge. The dredging action is intermittent and suitable only for easily flowing material.
Amphibious dredgers have the unusual feature of being able to work afloat or elevated clear of the water surface on legs. They can be equipped with grabs, buckets or a shovel installation.
All the above specialist types of dredger (and others) have been developed for specific situations and generally for small scale work such as narrow canals, industrial lagoons and reservoirs. Some types have been developed to handle contaminated sediments with minimum disturbance. They are not normally employed for large scale maintenance or capital dredging work.
A further type of dredger is the plough or bed leveller. This consists of a blade or bar which is pulled behind a suitable tug or work-boat. The method can be used for direct dredging over short distances and for levelling off the bed to the desired depth when a trailer or grab dredger is operating. It may also be used to pull material from close to quay walls and other places where a trailer cannot reach into a more accessible area. Sometimes the trailer itself operates the level1er if no tug or work-boat is available.
Air-lift dredgers are very similar to the jet-lift dredgers but the medium for inducing water and material flow is high pressure air injected at the month of the suction pipe. As with jet-lift dredgers there are no moving parts in the flow system. Hard or other difficult to loosen materials cannot be dredged.
Augur suction dredgers operate on the same principles as a cutter suction dredger, except that the mechanical cutting tool is a rotating Archimedean screw placed at right angles to the suction pipe. The screw dislodges material, which is fed to the centrally placed suction pipe. Most units have a shroud over the cutting screw which reduces the spread of the plume of disturbed bed material which normally escapes from all dredgers. The augur suction dredger advances.into the cutting face by hauling itself along a wire deployed directly ahead. Very accurate horizontal and vertical dimensions can be achieved.
Pneumatic dredgers work on the ‘evacuator’ principle. A chamber with inlets for bed material is pumped out with the inlets closed. The inlets are then opened and water and material drawn in. The mixture is then pumped out and the cycle repeated. The unit is generally suspended from a crane on land or from a small pontoon or barge. The dredging action is intermittent and suitable only for easily flowing material.
Amphibious dredgers have the unusual feature of being able to work afloat or elevated clear of the water surface on legs. They can be equipped with grabs, buckets or a shovel installation.
All the above specialist types of dredger (and others) have been developed for specific situations and generally for small scale work such as narrow canals, industrial lagoons and reservoirs. Some types have been developed to handle contaminated sediments with minimum disturbance. They are not normally employed for large scale maintenance or capital dredging work.
A further type of dredger is the plough or bed leveller. This consists of a blade or bar which is pulled behind a suitable tug or work-boat. The method can be used for direct dredging over short distances and for levelling off the bed to the desired depth when a trailer or grab dredger is operating. It may also be used to pull material from close to quay walls and other places where a trailer cannot reach into a more accessible area. Sometimes the trailer itself operates the level1er if no tug or work-boat is available.
.
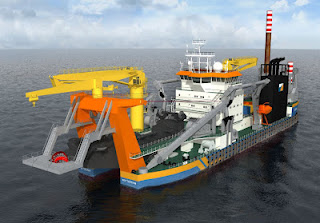
BACKHOE/DIPPER DREDGER
Backhoe and dipper dredgers again consist of a rectangular pontoon, on which is mounted the excavator unit. The excavator can be either an integral part of the dredger or a proprietary mobile type adapted for marine working. Material is excavated using a bucket of size compatible with the in-situ strength of the material being dredged. The excavated material is either loaded into barges or placed ashore. The older form of this type of dredger, the dipper or face shovel, used a wire operated integral excavator and was very heavily built to allow for dredging of hard materials such as old masonry and unblasted rock.
The wire operated excavator unit has now been largely superseded by hydraulically operated backhoe machines. These operate more efficiently than the face shovel. The size of a backhoe dredger is described by the bucket capacity, which can vary between 0.5 and 13 m3. Production is dependent upon bucket size and the hardness of the material. Breakout forces in excess of 90 t can be exerted by the larger machines, and because of the very high horizontal loads developed by the jigging action the backhoe dredger usually works on spuds. These are heavy pile-like structures which can be dropped into the sea-bed by the dredger. Two spuds are mounted at the digging end of the backhoe pontoon to provide resistance and one backhoe excavator is very efficient and has good vertical and horizontal control; carefully worked it will produce a smooth profile. Because the bucket is heavy and relatively rigid, care needs to be taken to avoid damage to such features as quay walls and canal linings.
The wire operated excavator unit has now been largely superseded by hydraulically operated backhoe machines. These operate more efficiently than the face shovel. The size of a backhoe dredger is described by the bucket capacity, which can vary between 0.5 and 13 m3. Production is dependent upon bucket size and the hardness of the material. Breakout forces in excess of 90 t can be exerted by the larger machines, and because of the very high horizontal loads developed by the jigging action the backhoe dredger usually works on spuds. These are heavy pile-like structures which can be dropped into the sea-bed by the dredger. Two spuds are mounted at the digging end of the backhoe pontoon to provide resistance and one backhoe excavator is very efficient and has good vertical and horizontal control; carefully worked it will produce a smooth profile. Because the bucket is heavy and relatively rigid, care needs to be taken to avoid damage to such features as quay walls and canal linings.
b. Hydraulic Dredger
The principal feature of all dredgers in this category is that the loosened material is raised from its in-situ state in suspension through a pipe system connected to a centrifugal pump. Various means can be employed to achieve the initial loosening of the material. If it is naturally very loose, suction alone may be sufficient, but firmer material may require mechanical loosening or the use of water jets. Hydraulic dredging is most efficient when working with fine materials, because they can easily be held in suspension. Coarser materials – and even gravel – can be worked but with a for greater demand on pump power and with greater wear on pumps and pipes.
SUCTION DREDGER
A stationary dredger used to mine for sand. The suction pipe is pushed vertically into a sand deposited. If necessary water jets help to bring the sand up. It is loaded into barges or pumped via pipeline directly to the reclamation area.
PROFILE OR PLAIN SUCTION DREDGER
In its most simple form this type consists of a pontoon able to support a pump and suction pipe and to make the connection to the discharge pipe. More sophisticated vessels have separate suction and delivery pumps, water jets at the suction inlet and articulated suction pipes. While working, a dredger may be held in position by one or more spuds or, in deeper water, by a complex system of moorings. Plain suction dredgers are mainly used to win fill material for reclamation, with the material being placed ashore through a floating pipeline. Very long distances can be pumped by the addition of booster pumps in the line. Material may alternatively be loaded directly into barges moored alongside. The normal measures of size are the diameter of the discharge pipe, which can vary between 100 and 1000 mm, or the installed horsepower.
Another use of plain suction dredgers – common in the USA – is to dredge from the navigation channel of a river and side cast the material to nearer the bank through a short pipeline or simply by jetting. In this role they are more commonly known as dust-pan dredgers.
Modern suction dredgers can recover material from great depths and can also extract sand from below a clay overburden. Known as a deep suction dredger, this type offers the potential to recover fill material from depths up to 100 m. Production is very dependent upon the permeability of the material dredged and is best in clean sands.
CUTTER SUCTION DREDGER
A stationary dredger which makes use of a cutter head to loosen the material to be dredged. It pumps the dredged material via a pipeline ashore or into barges. While dredging the cutter head describes arcs and is swung around the spudpole powered by winches. The cutter head can be replaced by several kinds of suction heads for special purposes, such as environmental dredging.
When the in-situ material is too compact to be removed by suction action alone, some form of mechanical loosening must be incorporated near the suction mouth. The most common method is a rotating cutter; the main feature of the cutter suction dredger. This is mounted at the lower end of the ladder used to support the cutter drive and the suction pipe. The loosened material then enters the suction mouth, passes through the suction pipe and pump (or pumps) and into the delivery line.
Cutter suction dredgers operate by swinging about a central working spud using moorings leading from the lower end of the ladder to anchors. By pulling on alternate sides the dredger clears an arc of cut, and then moves forward by pushing against the working spud using a spud carriage. A generally smooth bottom can be achieved, and modern instrumentation allows profiles and side slopes to be dredged accurately. Some of the larger cutter suction dredgers are self-propelled to allow easy movement from site to site.
The size of a cutter suction dredger is measured by the diameter of the suction pipe and by the installed machinery power. Pipe diameters are in the range 100 to 1500 mm. A modern highly automated cutter suction dredger is capable of achieving high outputs over sustained periods and production rates of around 500000 m3/week are possible under good conditions.
Cutter suction dredgers can be used to deliver through a pipe- line or to load barges. They may also be used simply as loosening devices for material to be re-handled by another type of dredger, in which mode discharge is directly over the stern to the sea. Pipeline discharge is most common but is vulnerable to waves and currents and causes an obstruction to other vessels. To avoid these problems part of the pipeline may be submerged and laid on the channel-or sea-bed.
Cutter suction dredgers are mainly used for capital dredging, especially when reclamation is associated with the dredging. Smaller vessels can be dismantled into sections and moved by road or rail for work in inland waterways, sludge lagoons, reservoirs and similar isolated areas. Large heavy-duty cutter dredgers are capable of dredging some types of rock which have not been pre-treated.
An alternative form of loosening is the use of a rotating bucket wheel at the suction mouth. Bucket wheel dredgers are most commonly used in mineral dredging operations and to date have not found general favour among the major international dredging contractors.
TRAILING SUCTION HOPPER DREDGER
A self propelled ship which fills its hold or hopper during dredging, while following a pre-set track. The hopper can be emptied by o bottom doors or valves (dumping) or by pumping its load ashore. This kind of dredger is mainly used in open water: rivers, canals, estuaries and the open sea.
Trailing suction hopper dredgers, commonly known simply as ‘hoppers’ or ‘trailers’, have a hull in the shape of a conventional ship, and are both highly seaworthy and able to operate without any form of mooring or spud. They are equipped with either single or twin (one on each side) trailing suction pipes. Material is lifted through the trailing pipes by one or more pumps and discharged into a hopper contained within the hull of the dredger. The measure of size of a hopper or trailer dredger is the hopper capacity. This may range from a few hundred cubic metres to over 20000 m’ – increasingly larger vessels have been constructed in recent years to allow economic transport of the dredged material, especially for reclamation projects.
The suction pipe terminates in a draghead, which may be of the plain type or may incorporate a water jet system, blades or teeth, or other means of dislodging compacted material. The function of the draghead is to allow the material to flow to the suction inlet as efficiently as possible.
A trailing suction hopper dredger operates very much like a floating vacuum cleaner. It sails slowly over the area to be dredged filling its hopper as it proceeds. On completion of loading the dredger sails to the disposal site where the cargo can be discharged, either by opening the doors or valves in the hopper bottom, by using the dredging pump to deliver to a shore pipeline, or directly to shore by using a special bow jet. This last technique is known as rainbowing and is commonly used for reclamation and beach nourishment.
Some trailer dredgers split over their entire length to achieve a rapid discharge of material which may be difficult to discharge through doors. Such special vessels are understandably more expensive to build than those with a rigid hull.
Trailing suction hopper dredgers operate best by skimming off layers of material in long runs, such as might be found in channel dredging. They are unable to get into corners and may be difficult to manœuvre in confined spaces close to quays and jetties. They are not very effective on hard materials such as the stiffer clays, but can dredge rock which has been blasted, or loosened by a cutter dredger. These dredgers are very efficient for the materials they can handle effectively. Most harbour maintenance dredging today is carried out by trailers, and they are also employed for capital projects, pipe trenching and reclamation.
RECLAMATION DREDGER
A stationary dredger used to empty hopper barges. A suction pipe is lowered into the barge. Extra water can be added by water by water jets to facilitate the suction process. The dredged material is pumped by pipeline ashore, to a reclamation area, or to a storage depot.
BARGE UNLOADING DREDGER
Barge unloading dredgers are used to transfer material from hopper barges to shore, usually for reclamation. A barge unloader is basically a pontoon supporting a suction pump for the discharge, and a high pressure water pump used to fluidize the barge contents by jetting. The mixture is then pumped through a pipeline to the point of reclamation or disposal.
c. Other types of Dredger
Specialized types of dredger are usually of small size and output. They include simple jet-lift and air-lift, auger suction, pneumatic and amphibious dredgers.
Jet-lift dredgers use the Venturi effect of a concentrated high-speed stream of water to draw the adjacent water, together with bed material, into a delivery pipe. The jet head has no moving parts so blockage by wires and other dock debris is minimized. These dredgers are relatively small units and some can be manoeuvred on spuds alone.
Air-lift dredgers are very similar to the jet-lift dredgers but the medium for inducing water and material flow is high pressure air injected at the month of the suction pipe. As with jet-lift dredgers there are no moving parts in the flow system. Hard or other difficult to loosen materials cannot be dredged.
Augur suction dredgers operate on the same principles as a cutter suction dredger, except that the mechanical cutting tool is a rotating Archimedean screw placed at right angles to the suction pipe. The screw dislodges material, which is fed to the centrally placed suction pipe. Most units have a shroud over the cutting screw which reduces the spread of the plume of disturbed bed material which normally escapes from all dredgers. The augur suction dredger advances.into the cutting face by hauling itself along a wire deployed directly ahead. Very accurate horizontal and vertical dimensions can be achieved.
Pneumatic dredgers work on the ‘evacuator’ principle. A chamber with inlets for bed material is pumped out with the inlets closed. The inlets are then opened and water and material drawn in. The mixture is then pumped out and the cycle repeated. The unit is generally suspended from a crane on land or from a small pontoon or barge. The dredging action is intermittent and suitable only for easily flowing material.
Amphibious dredgers have the unusual feature of being able to work afloat or elevated clear of the water surface on legs. They can be equipped with grabs, buckets or a shovel installation.
All the above specialist types of dredger (and others) have been developed for specific situations and generally for small scale work such as narrow canals, industrial lagoons and reservoirs. Some types have been developed to handle contaminated sediments with minimum disturbance. They are not normally employed for large scale maintenance or capital dredging work.
A further type of dredger is the plough or bed leveller. This consists of a blade or bar which is pulled behind a suitable tug or work-boat. The method can be used for direct dredging over short distances and for levelling off the bed to the desired depth when a trailer or grab dredger is operating. It may also be used to pull material from close to quay walls and other places where a trailer cannot reach into a more accessible area. Sometimes the trailer itself operates the level1er if no tug or work-boat is available.
WATER INJECTION DREDGER
A self propelled dredger which brings the sediment to be excavated into suspension with waterjets. This suspension is denser than water. It will be carried away by gravity and currents. Water injection dredging is mainly used for maintenance in harbours.
A relatively recent development in dredging equipment is the water injection dredger. This can be very effective in some material in order to fluidize it and create a turbidity current of higher density than the surrounding water. The bed material then moves in its own current. The system works best in mud and fine sand beds and has been used successfully in a number of port areas. Careful assessment must be made of the likely destination of the turbid water.
d. Auxiliaries
All modern dredgers are equipped with a range of sophisticated electronic control and data-logging systems appropriate to their type. These assist with positioning, loading and recording. VDU displays showing the position and attitude of a trailer draghead, cutter head, backhoe stick and bucket, or even a grab are set in front of the operator. Similar displays show in plan the location of the dredger and, where appropriate, its track and heading. Depth of cut, current dredged depth and slopes are also displayed on the same or separate monitors.
All these aids lead to increased efficiency of operation as they minimize overdredging. They reduce unnecessary travel or coverage (traversing an area already to profile) and improve the precision of dumping, particularly when forming the lower layers of a reclamation or where strict environmental controls exist.
e. Conclusion
Many different types of dredger exist, each with its advantages and disadvantages. The final choice of dredger for any cost and availability. Unless there are specific reasons for not using a particular type of dredger, the choice of type, size and number usually lies with the operator or contractor.
A self propelled dredger which brings the sediment to be excavated into suspension with waterjets. This suspension is denser than water. It will be carried away by gravity and currents. Water injection dredging is mainly used for maintenance in harbours.
A relatively recent development in dredging equipment is the water injection dredger. This can be very effective in some material in order to fluidize it and create a turbidity current of higher density than the surrounding water. The bed material then moves in its own current. The system works best in mud and fine sand beds and has been used successfully in a number of port areas. Careful assessment must be made of the likely destination of the turbid water.
d. Auxiliaries
All modern dredgers are equipped with a range of sophisticated electronic control and data-logging systems appropriate to their type. These assist with positioning, loading and recording. VDU displays showing the position and attitude of a trailer draghead, cutter head, backhoe stick and bucket, or even a grab are set in front of the operator. Similar displays show in plan the location of the dredger and, where appropriate, its track and heading. Depth of cut, current dredged depth and slopes are also displayed on the same or separate monitors.
All these aids lead to increased efficiency of operation as they minimize overdredging. They reduce unnecessary travel or coverage (traversing an area already to profile) and improve the precision of dumping, particularly when forming the lower layers of a reclamation or where strict environmental controls exist.
e. Conclusion
Many different types of dredger exist, each with its advantages and disadvantages. The final choice of dredger for any cost and availability. Unless there are specific reasons for not using a particular type of dredger, the choice of type, size and number usually lies with the operator or contractor.
WATER INJECTION DREDGER
A self propelled dredger which brings the sediment to be excavated into suspension with waterjets. This suspension is denser than water. It will be carried away by gravity and currents. Water injection dredging is mainly used for maintenance in harbours.
A relatively recent development in dredging equipment is the water injection dredger. This can be very effective in some material in order to fluidize it and create a turbidity current of higher density than the surrounding water. The bed material then moves in its own current. The system works best in mud and fine sand beds and has been used successfully in a number of port areas. Careful assessment must be made of the likely destination of the turbid water.
d. Auxiliaries
All modern dredgers are equipped with a range of sophisticated electronic control and data-logging systems appropriate to their type. These assist with positioning, loading and recording. VDU displays showing the position and attitude of a trailer draghead, cutter head, backhoe stick and bucket, or even a grab are set in front of the operator. Similar displays show in plan the location of the dredger and, where appropriate, its track and heading. Depth of cut, current dredged depth and slopes are also displayed on the same or separate monitors.
All these aids lead to increased efficiency of operation as they minimize over dredging. They reduce unnecessary travel or coverage (traversing an area already to profile) and improve the precision of dumping, particularly when forming the lower layers of a reclamation or where strict environmental controls exist.
e. Conclusion
Many different types of dredger exist, each with its advantages and disadvantages. The final choice of dredger for any cost and availability. Unless there are specific reasons for not using a particular type of dredger, the choice of type, size and number usually lies with the operator or contractor.
A stationary dredger used to mine for sand. The suction pipe is pushed vertically into a sand deposited. If necessary water jets help to bring the sand up. It is loaded into barges or pumped via pipeline directly to the reclamation area.
A self propelled ship which fills its hold or hopper during dredging, while following a pre-set track. The hopper can be emptied by o bottom doors or valves (dumping) or by pumping its load ashore. This kind of dredger is mainly used in open water: rivers, canals, estuaries and the open sea.
Trailing suction hopper dredgers, commonly known simply as ‘hoppers’ or ‘trailers’, have a hull in the shape of a conventional ship, and are both highly seaworthy and able to operate without any form of mooring or spud. They are equipped with either single or twin (one on each side) trailing suction pipes. Material is lifted through the trailing pipes by one or more pumps and discharged into a hopper contained within the hull of the dredger. The measure of size of a hopper or trailer dredger is the hopper capacity. This may range from a few hundred cubic metres to over 20000 m’ – increasingly larger vessels have been constructed in recent years to allow economic transport of the dredged material, especially for reclamation projects.
The suction pipe terminates in a draghead, which may be of the plain type or may incorporate a water jet system, blades or teeth, or other means of dislodging compacted material. The function of the draghead is to allow the material to flow to the suction inlet as efficiently as possible.
A trailing suction hopper dredger operates very much like a floating vacuum cleaner. It sails slowly over the area to be dredged filling its hopper as it proceeds. On completion of loading the dredger sails to the disposal site where the cargo can be discharged, either by opening the doors or valves in the hopper bottom, by using the dredging pump to deliver to a shore pipeline, or directly to shore by using a special bow jet. This last technique is known as rainbowing and is commonly used for reclamation and beach nourishment.
Some trailer dredgers split over their entire length to achieve a rapid discharge of material which may be difficult to discharge through doors. Such special vessels are understandably more expensive to build than those with a rigid hull.
Trailing suction hopper dredgers operate best by skimming off layers of material in long runs, such as might be found in channel dredging. They are unable to get into corners and may be difficult to manœuvre in confined spaces close to quays and jetties. They are not very effective on hard materials such as the stiffer clays, but can dredge rock which has been blasted, or loosened by a cutter dredger. These dredgers are very efficient for the materials they can handle effectively. Most harbour maintenance dredging today is carried out by trailers, and they are also employed for capital projects, pipe trenching and reclamation.
RECLAMATION DREDGER
A stationary dredger used to empty hopper barges. A suction pipe is lowered into the barge. Extra water can be added by water by water jets to facilitate the suction process. The dredged material is pumped by pipeline ashore, to a reclamation area, or to a storage depot.
BARGE UNLOADING DREDGER
Barge unloading dredgers are used to transfer material from hopper barges to shore, usually for reclamation. A barge unloader is basically a pontoon supporting a suction pump for the discharge, and a high pressure water pump used to fluidize the barge contents by jetting. The mixture is then pumped through a pipeline to the point of reclamation or disposal.
c. Other types of Dredger
Specialized types of dredger are usually of small size and output. They include simple jet-lift and air-lift, auger suction, pneumatic and amphibious dredgers.
Jet-lift dredgers use the Venturi effect of a concentrated high-speed stream of water to draw the adjacent water, together with bed material, into a delivery pipe. The jet head has no moving parts so blockage by wires and other dock debris is minimized. These dredgers are relatively small units and some can be manoeuvred on spuds alone.
Air-lift dredgers are very similar to the jet-lift dredgers but the medium for inducing water and material flow is high pressure air injected at the month of the suction pipe. As with jet-lift dredgers there are no moving parts in the flow system. Hard or other difficult to loosen materials cannot be dredged.
Augur suction dredgers operate on the same principles as a cutter suction dredger, except that the mechanical cutting tool is a rotating Archimedean screw placed at right angles to the suction pipe. The screw dislodges material, which is fed to the centrally placed suction pipe. Most units have a shroud over the cutting screw which reduces the spread of the plume of disturbed bed material which normally escapes from all dredgers. The augur suction dredger advances.into the cutting face by hauling itself along a wire deployed directly ahead. Very accurate horizontal and vertical dimensions can be achieved.
Pneumatic dredgers work on the ‘evacuator’ principle. A chamber with inlets for bed material is pumped out with the inlets closed. The inlets are then opened and water and material drawn in. The mixture is then pumped out and the cycle repeated. The unit is generally suspended from a crane on land or from a small pontoon or barge. The dredging action is intermittent and suitable only for easily flowing material.
Amphibious dredgers have the unusual feature of being able to work afloat or elevated clear of the water surface on legs. They can be equipped with grabs, buckets or a shovel installation.
All the above specialist types of dredger (and others) have been developed for specific situations and generally for small scale work such as narrow canals, industrial lagoons and reservoirs. Some types have been developed to handle contaminated sediments with minimum disturbance. They are not normally employed for large scale maintenance or capital dredging work.
A further type of dredger is the plough or bed leveller. This consists of a blade or bar which is pulled behind a suitable tug or work-boat. The method can be used for direct dredging over short distances and for levelling off the bed to the desired depth when a trailer or grab dredger is operating. It may also be used to pull material from close to quay walls and other places where a trailer cannot reach into a more accessible area. Sometimes the trailer itself operates the level1er if no tug or work-boat is available.
WATER INJECTION DREDGER
A self propelled dredger which brings the sediment to be excavated into suspension with waterjets. This suspension is denser than water. It will be carried away by gravity and currents. Water injection dredging is mainly used for maintenance in harbours.
A relatively recent development in dredging equipment is the water injection dredger. This can be very effective in some material in order to fluidize it and create a turbidity current of higher density than the surrounding water. The bed material then moves in its own current. The system works best in mud and fine sand beds and has been used successfully in a number of port areas. Careful assessment must be made of the likely destination of the turbid water.
d. Auxiliaries
All modern dredgers are equipped with a range of sophisticated electronic control and data-logging systems appropriate to their type. These assist with positioning, loading and recording. VDU displays showing the position and attitude of a trailer draghead, cutter head, backhoe stick and bucket, or even a grab are set in front of the operator. Similar displays show in plan the location of the dredger and, where appropriate, its track and heading. Depth of cut, current dredged depth and slopes are also displayed on the same or separate monitors.
All these aids lead to increased efficiency of operation as they minimize overdredging. They reduce unnecessary travel or coverage (traversing an area already to profile) and improve the precision of dumping, particularly when forming the lower layers of a reclamation or where strict environmental controls exist.
e. Conclusion
Many different types of dredger exist, each with its advantages and disadvantages. The final choice of dredger for any cost and availability. Unless there are specific reasons for not using a particular type of dredger, the choice of type, size and number usually lies with the operator or contractor.
A stationary dredger used to empty hopper barges. A suction pipe is lowered into the barge. Extra water can be added by water by water jets to facilitate the suction process. The dredged material is pumped by pipeline ashore, to a reclamation area, or to a storage depot.
A self propelled dredger which brings the sediment to be excavated into suspension with waterjets. This suspension is denser than water. It will be carried away by gravity and currents. Water injection dredging is mainly used for maintenance in harbours.
a. Mechanical Dredger
Mechanical dredgers come in a variety of forms, each involving the use of grab or bucket to loosen the in-situ material and raise and transport it to the surface.
BUCKET DREDGER
A stationary dredger, fixed on anchors and moved while dredging along semi-arcs by winches. The bucket dredger is one of the oldest types of dredging equipment. It has an endless chain of buckets, that fill while scraping over the bottom. The buckets are turned upside down and empty moving over the tumbler at the top. The dredged material is loaded in barges.
Bucket ladder dredgers are one of the oldest types of dredger. They usually comprise a rectangular pontoon with a central well in which a heavy steel frame or ladder is suspended. The ladder supports an endless chain of buckets, each of which is equipped with a cutting edge. By rotating the bucket chain about flat-sided wheels (known as tumblers) at each end of the ladder, material can be loosened and transported. A small proportion of the dredgers of this type are self-propelled. The propulsion machinery is used to move the vessel from site to site, but is not used in the dredging operation.
The dredging action starts when a bucket reaches the bottom of the ladder, where it loosens and scoops up a quantity of material. This material is carried in the bucket to the top of the ladder where, at the highest point of the chain, the bucket overturns and the contents are discharged. The material falls into drop chutes and into a barge moored alongside the dredger. Each bucket then returns empty on the underside of the chain to the bottom of the ladder where the cycle begins again. The size of a bucket dredger is usually described by the capacity of the buckets, which is in the range 100-900 litres.
Bucket ladder dredgers are able to dredge almost any material up to the point where blasting is required, and if fitted with ripper teeth may even be directly able to dredge weak rock. A minimal amount of water is added to the dredged material during careful use of the buckets. This is advantageous to production and costs, especially when dredging in silt and mud.
In operation, a bucket ladder dredger is held accurately in position by up to six moorings or anchors and the bucket ladder moved from side to side to excavate material. The mooring wires can obstruct other shipping, and high noise levels are a common problem if special steps are not taken to control sound emissions. Much of the power of a bucket dredger is used in turning the chain, but the high inertia of this can also assist in overcoming localized hard spots. The maximum weekly output of a bucket dredger can vary between 10.000 and 100.000 m3 (in-situ) depending upon size, location and material. Maximum dredging depths are normally around 20 m. Bucket ladder dredgers are complex and expensive machines to operate but can dredge to the required depth very accurately.
GRAB DREDGER
A stationary dredger, moored on anchors or on spudpoles. The dredging tool is a grab normally consisting of two halfshells operated by wires or (electro)-hydraulically. The grab can be mounted on a dragline or on a hydraulic excavator of the backhoe type. Many modifications of grabs have been constructed like (top) open grab, (top) closed grabs and watertight grabs. The grab dredger is used in harbours; the dragline type also in deep water. The dredged material is loaded in barges.
Grab dredgers, sometimes called clamshells, can exist in pontoon and self-propelled forms, the latter usually including a hopper within the vessel. The pontoon type grab dredger again comprises a rectangular pontoon on which is mounted a revolving crane equipped with a grab. The dredging operation consists of lowering the grab to the bottom, closing the grab, raising the filled grab to the surface and discharging the contents into a barge or, if appropriate, onto the adjoining bank. The size of this type is determined by the capacity of the grab bucket, which can vary between 1.0 and 20 m3 , depending upon the crane power.
The self-propelled grab hopper dredger is basically a ship which has one or more dredging cranes mounted around a receiving hopper. It is easily moved from site to site under its own power and also transports the dredged material to the disposal area. The size of this type of dredger is expressed in terms of the hopper capacity and can range from 100 to about 2.500 m3. The smaller vessels have a single crane, but some of the larger craft have up to four. Production depends upon crane and grab size, water depth and, in the case of the self-propelled variety, on the distance to the material disposal site.
Grab dredgers are usually held in position while working by anchors and moorings but a few are fitted with a spud, or pile, which can be dropped onto the bottom while the dredger is operating.
A wire line grab generally produces an irregular bottom profile with peaks and troughs and is thus most suited to bulk excavation. The grab is a relatively simple and inexpensive machine and performs best in consolidated silt, clays and loose sand, but the large, heavy versions are good for removing rubbish, old piles, rubble and similar obstructions. Grabs can also be used effectively for removing material from close to quay walls and in corners of docks and basins that are otherwise difficult to access.
A basic grab dredger can be quickly and economically made tip from conventional land machines securely fixed to pontoons for short term adhoc tasks, but care needs to be taken to check stability.
BACKHOE DREDGER
A stationary dredger, moved on anchors or on spudpoles. A spud is a large pole that can anchor a ship while allowing a rotating movement around the point of anchorage. Small backhoe dredgers can be track mounted and work from the banks of ditches. A backhoe dredger is a hydraulic excavator equipped with a half open shell. This shell is filled moving towards the machine. Usually the dredged material is loaded in barges. This machine is mainly used in harbours and other shallow waters
.
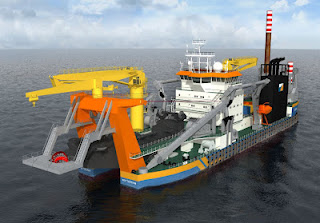
BACKHOE/DIPPER DREDGER
Backhoe and dipper dredgers again consist of a rectangular pontoon, on which is mounted the excavator unit. The excavator can be either an integral part of the dredger or a proprietary mobile type adapted for marine working. Material is excavated using a bucket of size compatible with the in-situ strength of the material being dredged. The excavated material is either loaded into barges or placed ashore. The older form of this type of dredger, the dipper or face shovel, used a wire operated integral excavator and was very heavily built to allow for dredging of hard materials such as old masonry and unblasted rock.
The wire operated excavator unit has now been largely superseded by hydraulically operated backhoe machines. These operate more efficiently than the face shovel. The size of a backhoe dredger is described by the bucket capacity, which can vary between 0.5 and 13 m3. Production is dependent upon bucket size and the hardness of the material. Breakout forces in excess of 90 t can be exerted by the larger machines, and because of the very high horizontal loads developed by the jigging action the backhoe dredger usually works on spuds. These are heavy pile-like structures which can be dropped into the sea-bed by the dredger. Two spuds are mounted at the digging end of the backhoe pontoon to provide resistance and one backhoe excavator is very efficient and has good vertical and horizontal control; carefully worked it will produce a smooth profile. Because the bucket is heavy and relatively rigid, care needs to be taken to avoid damage to such features as quay walls and canal linings.
b. Hydraulic Dredger
The principal feature of all dredgers in this category is that the loosened material is raised from its in-situ state in suspension through a pipe system connected to a centrifugal pump. Various means can be employed to achieve the initial loosening of the material. If it is naturally very loose, suction alone may be sufficient, but firmer material may require mechanical loosening or the use of water jets. Hydraulic dredging is most efficient when working with fine materials, because they can easily be held in suspension. Coarser materials – and even gravel – can be worked but with a for greater demand on pump power and with greater wear on pumps and pipes.
SUCTION DREDGER
A stationary dredger used to mine for sand. The suction pipe is pushed vertically into a sand deposited. If necessary water jets help to bring the sand up. It is loaded into barges or pumped via pipeline directly to the reclamation area.
PROFILE OR PLAIN SUCTION DREDGER
In its most simple form this type consists of a pontoon able to support a pump and suction pipe and to make the connection to the discharge pipe. More sophisticated vessels have separate suction and delivery pumps, water jets at the suction inlet and articulated suction pipes. While working, a dredger may be held in position by one or more spuds or, in deeper water, by a complex system of moorings. Plain suction dredgers are mainly used to win fill material for reclamation, with the material being placed ashore through a floating pipeline. Very long distances can be pumped by the addition of booster pumps in the line. Material may alternatively be loaded directly into barges moored alongside. The normal measures of size are the diameter of the discharge pipe, which can vary between 100 and 1000 mm, or the installed horsepower.
Another use of plain suction dredgers – common in the USA – is to dredge from the navigation channel of a river and side cast the material to nearer the bank through a short pipeline or simply by jetting. In this role they are more commonly known as dust-pan dredgers.
Modern suction dredgers can recover material from great depths and can also extract sand from below a clay overburden. Known as a deep suction dredger, this type offers the potential to recover fill material from depths up to 100 m. Production is very dependent upon the permeability of the material dredged and is best in clean sands.
CUTTER SUCTION DREDGER
A stationary dredger which makes use of a cutter head to loosen the material to be dredged. It pumps the dredged material via a pipeline ashore or into barges. While dredging the cutter head describes arcs and is swung around the spudpole powered by winches. The cutter head can be replaced by several kinds of suction heads for special purposes, such as environmental dredging.
When the in-situ material is too compact to be removed by suction action alone, some form of mechanical loosening must be incorporated near the suction mouth. The most common method is a rotating cutter; the main feature of the cutter suction dredger. This is mounted at the lower end of the ladder used to support the cutter drive and the suction pipe. The loosened material then enters the suction mouth, passes through the suction pipe and pump (or pumps) and into the delivery line.
Cutter suction dredgers operate by swinging about a central working spud using moorings leading from the lower end of the ladder to anchors. By pulling on alternate sides the dredger clears an arc of cut, and then moves forward by pushing against the working spud using a spud carriage. A generally smooth bottom can be achieved, and modern instrumentation allows profiles and side slopes to be dredged accurately. Some of the larger cutter suction dredgers are self-propelled to allow easy movement from site to site.
The size of a cutter suction dredger is measured by the diameter of the suction pipe and by the installed machinery power. Pipe diameters are in the range 100 to 1500 mm. A modern highly automated cutter suction dredger is capable of achieving high outputs over sustained periods and production rates of around 500000 m3/week are possible under good conditions.
Cutter suction dredgers can be used to deliver through a pipe- line or to load barges. They may also be used simply as loosening devices for material to be re-handled by another type of dredger, in which mode discharge is directly over the stern to the sea. Pipeline discharge is most common but is vulnerable to waves and currents and causes an obstruction to other vessels. To avoid these problems part of the pipeline may be submerged and laid on the channel-or sea-bed.
Cutter suction dredgers are mainly used for capital dredging, especially when reclamation is associated with the dredging. Smaller vessels can be dismantled into sections and moved by road or rail for work in inland waterways, sludge lagoons, reservoirs and similar isolated areas. Large heavy-duty cutter dredgers are capable of dredging some types of rock which have not been pre-treated.
An alternative form of loosening is the use of a rotating bucket wheel at the suction mouth. Bucket wheel dredgers are most commonly used in mineral dredging operations and to date have not found general favour among the major international dredging contractors.
TRAILING SUCTION HOPPER DREDGER
A self propelled ship which fills its hold or hopper during dredging, while following a pre-set track. The hopper can be emptied by o bottom doors or valves (dumping) or by pumping its load ashore. This kind of dredger is mainly used in open water: rivers, canals, estuaries and the open sea.
Trailing suction hopper dredgers, commonly known simply as ‘hoppers’ or ‘trailers’, have a hull in the shape of a conventional ship, and are both highly seaworthy and able to operate without any form of mooring or spud. They are equipped with either single or twin (one on each side) trailing suction pipes. Material is lifted through the trailing pipes by one or more pumps and discharged into a hopper contained within the hull of the dredger. The measure of size of a hopper or trailer dredger is the hopper capacity. This may range from a few hundred cubic metres to over 20000 m’ – increasingly larger vessels have been constructed in recent years to allow economic transport of the dredged material, especially for reclamation projects.
The suction pipe terminates in a draghead, which may be of the plain type or may incorporate a water jet system, blades or teeth, or other means of dislodging compacted material. The function of the draghead is to allow the material to flow to the suction inlet as efficiently as possible.
A trailing suction hopper dredger operates very much like a floating vacuum cleaner. It sails slowly over the area to be dredged filling its hopper as it proceeds. On completion of loading the dredger sails to the disposal site where the cargo can be discharged, either by opening the doors or valves in the hopper bottom, by using the dredging pump to deliver to a shore pipeline, or directly to shore by using a special bow jet. This last technique is known as rainbowing and is commonly used for reclamation and beach nourishment.
Some trailer dredgers split over their entire length to achieve a rapid discharge of material which may be difficult to discharge through doors. Such special vessels are understandably more expensive to build than those with a rigid hull.
Trailing suction hopper dredgers operate best by skimming off layers of material in long runs, such as might be found in channel dredging. They are unable to get into corners and may be difficult to manœuvre in confined spaces close to quays and jetties. They are not very effective on hard materials such as the stiffer clays, but can dredge rock which has been blasted, or loosened by a cutter dredger. These dredgers are very efficient for the materials they can handle effectively. Most harbour maintenance dredging today is carried out by trailers, and they are also employed for capital projects, pipe trenching and reclamation.
RECLAMATION DREDGER
A stationary dredger used to empty hopper barges. A suction pipe is lowered into the barge. Extra water can be added by water by water jets to facilitate the suction process. The dredged material is pumped by pipeline ashore, to a reclamation area, or to a storage depot.
BARGE UNLOADING DREDGER
Barge unloading dredgers are used to transfer material from hopper barges to shore, usually for reclamation. A barge unloader is basically a pontoon supporting a suction pump for the discharge, and a high pressure water pump used to fluidize the barge contents by jetting. The mixture is then pumped through a pipeline to the point of reclamation or disposal.
c. Other types of Dredger
Specialized types of dredger are usually of small size and output. They include simple jet-lift and air-lift, auger suction, pneumatic and amphibious dredgers.
Jet-lift dredgers use the Venturi effect of a concentrated high-speed stream of water to draw the adjacent water, together with bed material, into a delivery pipe. The jet head has no moving parts so blockage by wires and other dock debris is minimized. These dredgers are relatively small units and some can be manoeuvred on spuds alone.
Air-lift dredgers are very similar to the jet-lift dredgers but the medium for inducing water and material flow is high pressure air injected at the month of the suction pipe. As with jet-lift dredgers there are no moving parts in the flow system. Hard or other difficult to loosen materials cannot be dredged.
Augur suction dredgers operate on the same principles as a cutter suction dredger, except that the mechanical cutting tool is a rotating Archimedean screw placed at right angles to the suction pipe. The screw dislodges material, which is fed to the centrally placed suction pipe. Most units have a shroud over the cutting screw which reduces the spread of the plume of disturbed bed material which normally escapes from all dredgers. The augur suction dredger advances.into the cutting face by hauling itself along a wire deployed directly ahead. Very accurate horizontal and vertical dimensions can be achieved.
Pneumatic dredgers work on the ‘evacuator’ principle. A chamber with inlets for bed material is pumped out with the inlets closed. The inlets are then opened and water and material drawn in. The mixture is then pumped out and the cycle repeated. The unit is generally suspended from a crane on land or from a small pontoon or barge. The dredging action is intermittent and suitable only for easily flowing material.
Amphibious dredgers have the unusual feature of being able to work afloat or elevated clear of the water surface on legs. They can be equipped with grabs, buckets or a shovel installation.
All the above specialist types of dredger (and others) have been developed for specific situations and generally for small scale work such as narrow canals, industrial lagoons and reservoirs. Some types have been developed to handle contaminated sediments with minimum disturbance. They are not normally employed for large scale maintenance or capital dredging work.
A further type of dredger is the plough or bed leveller. This consists of a blade or bar which is pulled behind a suitable tug or work-boat. The method can be used for direct dredging over short distances and for levelling off the bed to the desired depth when a trailer or grab dredger is operating. It may also be used to pull material from close to quay walls and other places where a trailer cannot reach into a more accessible area. Sometimes the trailer itself operates the level1er if no tug or work-boat is available.
WATER INJECTION DREDGER
A self propelled dredger which brings the sediment to be excavated into suspension with waterjets. This suspension is denser than water. It will be carried away by gravity and currents. Water injection dredging is mainly used for maintenance in harbours.
A relatively recent development in dredging equipment is the water injection dredger. This can be very effective in some material in order to fluidize it and create a turbidity current of higher density than the surrounding water. The bed material then moves in its own current. The system works best in mud and fine sand beds and has been used successfully in a number of port areas. Careful assessment must be made of the likely destination of the turbid water.
d. Auxiliaries
All modern dredgers are equipped with a range of sophisticated electronic control and data-logging systems appropriate to their type. These assist with positioning, loading and recording. VDU displays showing the position and attitude of a trailer draghead, cutter head, backhoe stick and bucket, or even a grab are set in front of the operator. Similar displays show in plan the location of the dredger and, where appropriate, its track and heading. Depth of cut, current dredged depth and slopes are also displayed on the same or separate monitors.
All these aids lead to increased efficiency of operation as they minimize overdredging. They reduce unnecessary travel or coverage (traversing an area already to profile) and improve the precision of dumping, particularly when forming the lower layers of a reclamation or where strict environmental controls exist.
e. Conclusion
Many different types of dredger exist, each with its advantages and disadvantages. The final choice of dredger for any cost and availability. Unless there are specific reasons for not using a particular type of dredger, the choice of type, size and number usually lies with the operator or contractor.